Quality
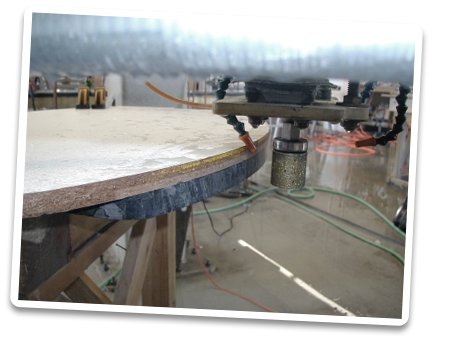
Fabrication Quality
There is a large variation in the quality produced by different fabrication shops. There are some relatively simple factors to check which will allow an inexperienced individual to rapidly ascertain the quality level of a given shop:
1. Stone Selection
The selection of your stone is the most critical aspect of an interior stone project. The industry is rife with horror stories about dissatisfied customers that were not properly educated by their fabricator or contractor. As a natural product stone has variations which are common but usually not in evidence on the small sample tiles people often use to pick a color. If at all possible a customer should inspect slabs and select the specific slabs for their job. In our experience customers will change their color from what was selected from samples over 75% of the time when given the opportunity to select their slabs. Participating in the selection of the slabs also insures that the various features of the stone do not come as an unpleasant surprise at install. If your fabricator does not want to help you with your stone selection find another!
2. Edge polish
Edges can be polished by hand, machine, or a combination. Regardless of the method employed the edge should be free from horizontal lines or dull areas which are often evident in poorly finished work. Hazy lines where top and bottom edge radiuses blend into flat areas are also an indicator of mediocre work. These lines or haze are not obvious to casual inspection but are readily apparent of the edge is inspected from several angles. A look down the finished edge should show a uniformly polished surface that is glassy smooth. Ripples, waves, bumps or divots are all evidence of inferior quality work.
3. Dimensional accuracy
Many shops still use freehand methods to generate sink cutouts and radius shapes. Hand generated curves are characterized by flat spots, ripples, bumps, and divots which are unavoidable on freehand work. A top quality sink cutout, radiused corner, or arc will be glassy smooth in appearance and to the touch. Dimensions on radiused corners should match exactly.
4. Undercutting
Natural stone slabs can vary by as much as 1/8” in thickness. A high quality fabricator will backgrind the underside of the stone so that the stone thickness across joints is an exact match.
5. Underside finish
The backside of polished slabs is very coarse. High quality fabricators will hone the exposed underside of overhangs to remove this coarse finish.
6. Joints
Due to the limitations of slab size most granite jobs will have seams. Good fabrication equipment will provide the fabricator with joint faces which are absolutely perpendicular and free of saw marks. The pieces at a joint should be touching with only a small visible seam which is formed by the small bevel on the top edge of the pieces. This bevel is necessary to remove the very small chips which occur when the granite is sawn. The seam most times will be flush although on occasion a small step is unavoidable when one or both pieces of the granite have a slight crown.
7. Sink Cutouts
The sink cutout is a very conspicuous feature of a stone countertop. For undermount sinks the cutout should match the sink shape exactly with a consistent overhang (or reveal) relative to the top of the vertical walls of the sink. When a shop freehands it’s sink cutouts the installer usually has to position the sink to “split the difference” between the shape of the sink and the dimensional inaccuracies in the freehand sink cutout. As noted previously the edges of the sink cutout should be free of lines, bumps, or divots.